サテリットの精密加工
超ミクロの精度は先進の技術から。
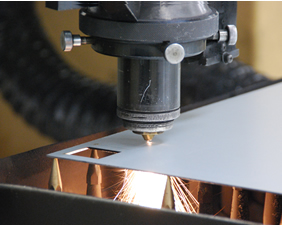
また、短納期品への対応につきましても、常に柔軟に対応できる生産体制を組み、受注から納入までのスピードアップを計り、 ユーザーのご要望にお応えしています。
概要
「どんなに微細でも」「どんなに高い精度でも」「どんな素材でも」「どんな加工方法でも」
弊社は貴社がお取引先からご満足頂くための「武器」として機能いたします。
株式会社サテリット
- 微細な加工の試作
- 精度の高い試作
- 多様な素材の試作
- 多様な加工方法の試作
- 20年間培ったノウハウ
貴社
- 企画した形状が予定の精度で製品化できるかを試せるメリット
- 試作の作成、評価の作業における効率化のメリット
- コストのメリット
- 時間のメリット
「高精度」で「多様」で「微細」な高付加価値のコネクタを迅速に開発・提供
アッセンブリ
メーカ等
貴社お取引先
弊社の特徴
- 微細な加工による試作がご提供できます
- ワイヤーの細い線(3/100)が使え、細いスリットが切れます(細い穴、細い残りもOKです)。
- 穴あけ機によりコンマ2のスリットを内側から切ることができます。
- 複雑で微細な曲げ加工ができます。
- コンマ3.5ミリの幅にコンマ2のリブを出すことができます。
- コンマ2ミリの幅の絞りを出すことができます。
- 精度の高い試作がご提供できます
-
- ワイヤー加工の精度が2/1000となっています。
- 精度を出すための最終チェックに適した簡易金型を作り精度を出しています。
- 素材や形状によって発生するスプリングバックなどを考慮した治工具をつくり、機械ではできない熟練工の手でなじませる作業により精度を出しています。
- 測定データを添付して図面どおりの精度であることを証明することができます。
- 多様な素材の試作がご提供できます
-
- 素材が金属なら超硬であっても超柔であっても加工できます。
- 薄さ3/100の薄といわれる素材でも切断、曲げ等の加工をすることができます。
- 厚さ200ミリの厚板でも切断することができます。
- 多くの種類の試作材料を在庫として持っておりまた、素材メーカとの連携によりあらゆる素材の試作を迅速にご提供することができます。
- 多様な加工方法により試作がご提供できます
- 複合加工(レーザー、ワイヤー、プレス、エッジングなど)による加工ができます。
- 外注との協力により機械加工(フライス、マシニング、旋盤)とワイヤーを組み合わせて加工することができます。
- 数量が多いときには、エッチング加工と曲げ加工により対応することができます。
- 鍍金、塗装、熱処理など他の処理も業者間ネットワークにより一貫して提供することができます。
- 20年間培ったノウハウをご提供できます
-
- 設計と製造のギャップをすり合わせて適切な試作を提供することができます。
- 設計者が気づかない、図面上ではわからない加工が困難な形状に対して瞬時に理解し、形状変更、展開変更を提案することができます。
- 簡易金型の使用で量産化の可能性を確認することができます。
- 素材の知識を保有しており、加工性の高い素材などを提案することができます。
- 小ロットであれば製品を作成することができます。
- プレスの量産品における追加工も対応しており、型の変更による試作作成の検討ができます。
- 短納期(早くて翌日、平均1週間)小ロット(1個から)で対応できます。
貴社のメリット
- 企画した形状が予定の精度で製品化できるかを試せるメリット
- 細線ワイヤーでの加工により小型化、精密化に対応した試作が獲得できます。
- コンマ2ミリメートルの小径穴(内側からのスリット)の試作を獲得できます。
- 板厚以下の狭ピッチのある試作を獲得できます。
- 小型、軽量、薄型、狭ピッチだけでなく厚板の試作を獲得できます。
- 小型の製品のリブ、曲げの試作が獲得できます。
- 切る精度2/1000、曲げ3/100の試作が獲得できます。
- アッセンブリーメーカーの規格通りあるいはそれ以上の精度のコネクタがつくれます。
- 試作の作成、評価の作業における効率化のメリット
-
- ワンストップで様々な加工の試作を獲得することができます。
- 適した素材(性質、硬度、加工の容易性、耐久、耐候、耐熱、絶縁など)や、考えもつかなかった素材の提案を受けることができます。
- 同じ形状で100分の2~3の寸法違いでの試作も可能なので、細かい比較まで可能になります。
- 量産に近い試作が獲得でき、試作の作成の回数も減らすことができるだけではく、耐久性等の試験において量産に近いデータを獲得することができます。
- 図面内容により、嵌合まで考えた物づくりをすることができます。
- 試作の修正で対応するか新規に製作するかの判断ができます。
- 設計のやり直しがなくなり、試作作成に関するやり取りの手間が省けます。
- コストのメリット
- 抜き型などがなくても作れるため、コストが下がり早く試作が手に入ります。
- 既存の試作の派生で試作を得ることができ、コスト削減ができます。
- 試作作成のやり直しが少なくなりコストが削減できます。
- 早い時期から量産の可能性がわかりコストが削減できます。
- 一か所に任せてしまえるので様々な作業コストが削減できます。
- 時間のメリット
-
- 早い試作を得られることで開発期間を短縮することができます。
- 既存の試作の派生(プレス品への追加加工など)で試作を得ることができ、時間短縮が図れます。
- 急な変更などには、簡易型を制作して追加工して試作を受けることができます。
- 短納期が求められるときに金型製造に時間がかかる時、1ロットだけエッジングで製品をつくるなどして初回使用分だけ手当てし、時間を稼ぐことができます。
- 豊富な種類の試作材料を保有しているので、短納期で対応できます。
精度が高く、多様で、付加価値のあるコネクタを、素早く開発提供できます。
他のコネクターメーカに対する優位性が確保できます。
アッセンブリーメーカ等から選ばれるコネクターメーカになることができます。
他のコネクターメーカに対する優位性が確保できます。
アッセンブリーメーカ等から選ばれるコネクターメーカになることができます。